Deciphering the Enigma of Porosity in Welding: Tips for Lessening Flaws and Making The Most Of Quality
In the detailed globe of welding, porosity continues to be a relentless obstacle that can significantly influence the high quality and integrity of welded joints. As we delve into the depths of porosity in welding, revealing the tricks to its avoidance and control will be vital for professionals looking for to grasp the art of high-grade weldments.
Understanding Porosity in Welding
Porosity in welding, an usual concern encountered by welders, refers to the existence of gas pockets or voids in the welded material, which can endanger the integrity and top quality of the weld. These gas pockets are typically entraped throughout the welding process due to numerous factors such as improper shielding gas, polluted base materials, or incorrect welding parameters. The development of porosity can weaken the weld, making it prone to splitting and corrosion, eventually resulting in structural failures.
Comprehending the origin of porosity is important for welders to successfully stop its event. By identifying the relevance of maintaining appropriate gas securing, making certain the tidiness of base materials, and maximizing welding setups, welders can significantly lower the chance of porosity development. Furthermore, making use of strategies like pre-heating the base product, employing correct welding methods, and performing thorough assessments post-welding can further help in lessening porosity flaws. On the whole, an extensive understanding of porosity in welding is necessary for welders to generate high-grade and long lasting welds.

Typical Reasons For Porosity
When inspecting welding procedures for prospective high quality problems, recognizing the typical reasons for porosity is important for maintaining weld honesty and avoiding architectural failings. Porosity, identified by the presence of tooth cavities or gaps in the weld metal, can significantly jeopardize the mechanical residential or commercial properties of a welded joint. One usual reason for porosity is incorrect protecting gas protection. Poor shielding gas flow prices or incorrect gas mixes can cause climatic contamination, causing porosity development.
In addition, welding at incorrect criteria, such as excessively high traveling speeds or currents, can generate too much disturbance in the weld pool, capturing gases and triggering porosity. By resolving these common reasons with appropriate gas securing, product preparation, and adherence to ideal welding specifications, welders can minimize porosity and boost the quality of their welds.
Methods for Porosity Avoidance
Applying efficient safety nets is crucial in lessening the occurrence of porosity in welding procedures. One method for porosity avoidance is ensuring correct cleaning of the base metal prior to welding. Contaminants such as oil, grease, corrosion, and paint can cause porosity, so thorough cleaning making use of proper solvents or mechanical techniques is crucial.

Making use of premium filler products and protecting gases that are ideal for the base metal and welding procedure can dramatically minimize the danger of porosity. Additionally, maintaining appropriate welding parameters, such as voltage, existing, travel speed, and gas circulation rate, is crucial for porosity avoidance.
Additionally, utilizing appropriate welding strategies, such as preserving a constant travel rate, electrode angle, and arc size, can help prevent porosity (What is Porosity). Adequate training of welders to ensure they comply with ideal methods and quality assurance treatments is likewise necessary in lessening porosity issues in welding

Finest Practices for Quality Welds
Ensuring adherence to industry requirements and proper weld joint prep work are essential elements of accomplishing consistently premium welds. Along with these foundational actions, there are several best practices that welders can execute to even more boost the high quality of their welds. One secret method is maintaining correct tidiness in the welding location. Contaminants such as oil, grease, corrosion, look what i found and paint can negatively affect the top quality of the weld, causing defects. Completely cleaning up the work surface and bordering area before welding can help reduce these issues.
An additional ideal method is to very carefully choose the ideal welding specifications for the certain products being signed up with. This includes setting the correct voltage, current, travel rate, and protecting gas flow price. Appropriate specification choice ensures optimal weld penetration, combination, and general high quality. In addition, utilizing premium welding consumables, such as electrodes and filler steels, can considerably influence the final weld quality. Purchasing costs consumables can lead to stronger, extra durable welds with less defects. By complying with these ideal techniques, welders can continue reading this continually produce top quality welds that fulfill industry requirements and go beyond client assumptions.
Relevance of Porosity Control
Porosity control plays a crucial function in making sure the stability and top quality of welding joints. Porosity, characterized by the existence of cavities or gaps within the weld steel, can substantially endanger the mechanical buildings and architectural honesty of the weld. Excessive porosity weakens the weld, making it much more susceptible to breaking, corrosion, and general failing under operational tons.
Reliable porosity control is necessary for maintaining the wanted mechanical residential or commercial properties, such as strength, ductility, and durability, of the welded joint. What is Porosity. By reducing porosity, welders can boost the total high quality and integrity of the weld, ensuring that it fulfills the performance demands of the intended application
Additionally, porosity control is crucial for achieving the preferred visual look of the weld. Excessive porosity not only damages the weld yet additionally detracts from its visual appeal, which can you could try here be essential in industries where looks are vital. Proper porosity control techniques, such as utilizing the appropriate shielding gas, controlling the welding parameters, and making certain correct tidiness of the base materials, are necessary for generating high-quality welds with marginal problems.
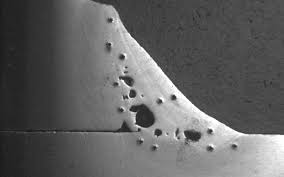
Conclusion
In conclusion, porosity in welding is an usual issue that can compromise the top quality of the weld. It is necessary to control porosity in welding to ensure the stability and toughness of the final product.